Research scientists writing in Nature Communications have said that switching to graphene protective coating on disk drive patters and read/write heads opens the way to 4–10 Tb/in2 areal density HDDs using HAMR and HAMR+bit patterned media.
Looking at the current 1 1Tb/in2 areal density used in 18TB, 9-platter drives with a 2TB/platter capacity, you could extrapolate the application of the tech as ushering in an era of, for example, 180TB 9-platter drives.
As the size of the bit area on a disk platter surface decreases, the signal showing its magnetic pole direction decreases in intensity: making it harder to detect. The signal amplitude can be increased if the read/write heads fly closer to the disk platter’s recording medium. Both the read/write head and the platter recording medium are protected by so-called carbon overcoat (COC) protection layers. Making the head-platter recording medium gap smaller means having thinner protection layers. But there will be problems with friction, wear, corrosion, and thermal stability if COC thickness goes under 2nm with HAMR recording technology.
The team, which included boffins from the National University of Singapore, the Argonne National Laboratory in the US, the CSIR-Advanced Materials and Processes Research Institute in India, and Cambridge and Exter in the UK, wrote that current COC thickness is 3nm and that is used to make disk drives with a 1Tb/in2 areal density (AD). Their paper includes a graphic showing a disk drive platter and read/write head gap:
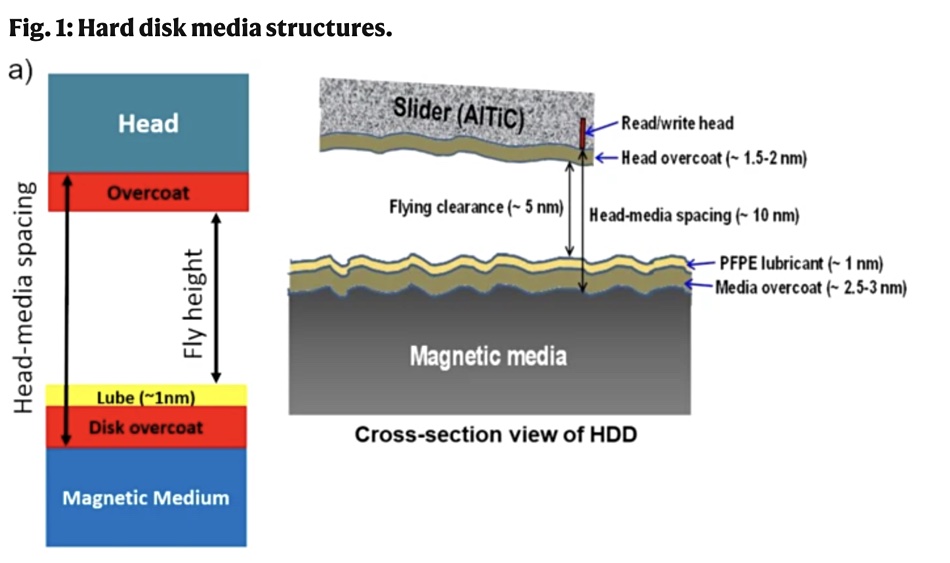
The paper’s authors noted: “A COC thickness <1 nm would be required for ~10 Tb/in2. However, current COCs lose most of their appealing properties, such as anti-friction, wear resistance, Young’s Modulus, and corrosion protection, when their thickness is below 2–3 nm.” [Young’s modulus is a measure of a material’s tensile stiffness.]
On top of this HAMR (Heat-Assisted Magnetic Recording) requires laser-produced heat to be applied to the bit areas to enable bit values to be written. COCs suffer degradation when their thickness goes under 4nm in HAMR conditions and the authors wrote “the overcoats for HAMR require thermal stability at least up to ~700–800 K to avoid degradation over time.”
Graphene, said to be 200 times stronger than steel, could be used instead of ordinary carbon as the protective overcoat. It is an alternative form of carbon with a single layer of carbon atoms arranged in a 2-dimensional hexagonal lattice.
They researchers investigated the use of 1–4 layers of chemical vapour deposition (CVD) grown graphene (1–4LG) with HAMR technology. They found very high wear-resistance, thermal stability, good corrosion resistance and anti-friction properties. The paper stated: “Thermal stability tests confirm that 1LG on FePt (Iron-Platinum) can withstand HAMR-like conditions, without degradation. Graphene’s superior performance and its thinness can enable the development of ultra-high-density magnetic data storage technologies.”
These include “bit patterned media (BPM), where the magnetic storage layer is patterned into an array of pillars, each representing a single bit.” In fact: “The combination of 1LG + HAMR + BPM may increase AD > 10 Tb/in2.”
We have tabulated the effects on disk drive capacity of increasing areal density by extrapolating from today’s 18TB, 9-platter drives using 1 Tb/in2 aerial density:
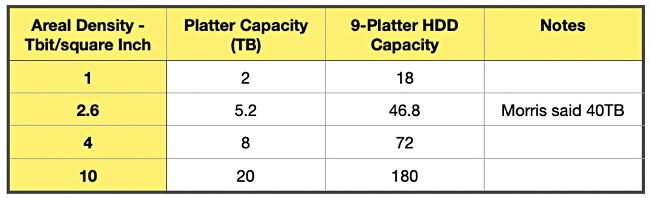
Seagate CTO John Morris told an investment analyst briefing in February that 2.6Tb/in2 is “capable of supporting 40TB in our nine-platter nearline drive.” A straight extrapolation would provide a 46.8TB drive. He discussed “the feasibility for achieving a product shipment of 50 terabytes by 2026.”
A 10 Tb/in2 aerial density implies that a 180TB, 9-platter disk drive could (in theory) be produced. This is beyond the HDD capacity projections mentioned in public by HDD makers. For example, Morris told the investment analysts: ”We have a path to 10 terabytes per disk [platter] by 2030, meaning a 90TB, 9-platter drive.”
That implies a 5Tb/in2 aerial density. The research scientists’ paper hypothesises that double that density is ultimately achievable by changing from carbon overcoats to graphene ones.
This assumes that HAMR and BPM technology can be developed appropriately, of course.
Boot note
Full text of the article is available here: Dwivedi, N., Ott, A.K., Sasikumar, K. et al. Graphene overcoats for ultra-high storage density magnetic media. Nat Commun 12, 2854 (2021).